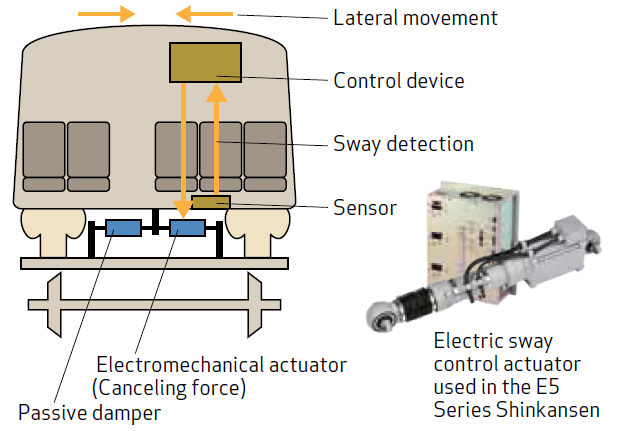
Through prototype evaluation, East Japan Railway engineers found that electromechanical actuators could be configured to be more compact, while providing good response and high thrust. Subsequently, an electromechanical actuator incorporating a planetary roller screw was determined through trial and error to be the optimal solution. In view of the relatively large number of mechanical parts involved, these planetary roller screw type actuators were endurance tested under a variety of conditions.
The operating principle of active sway control is as follows. An accelerometer detects lateral sway of the train carriage attributable to the rails, air flow, and other external factors. A controller then calculates the necessary thrust required to counter sway and this is sent to the actuator. Each bogey has one actuator and a passive damper to attenuate lateral vibration.
The passive damper provides the damping force when the electromechanical actuator is not activated, and decreases the damping force required when the actuator is activated in order to maximize its damping effect. As a result, passengers enjoy a comfortable ride at even at operating speeds of 320 km/h.
Moog Global Support
Our commitment to keep your motion control components and systems running at peak performance by providing responsive repair and O&M support. Around the globe in 24 countries, local teams of trained Moog technicians are on standby with the services you need from express repairs to exchange programs, and on-site technical support